Nanoteilchen nach einfacher Rezeptur
Roland Wengenmayr
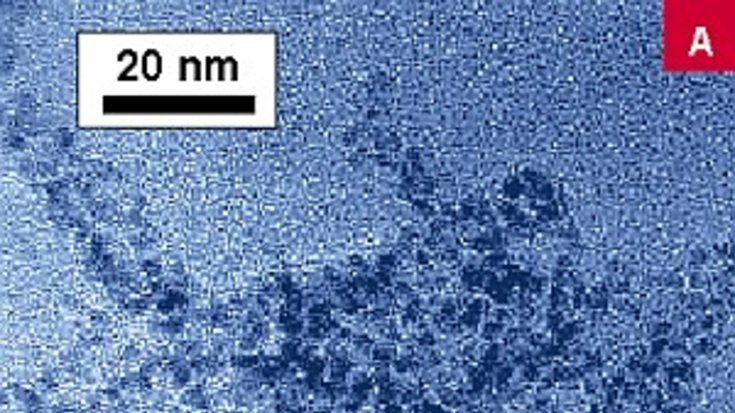
„Nanopartikel“ für Brennstoffzellen-Katalysatoren mit einem Durchmesser von wenigen Milliardstel Metern können neuerdings erstaunlich einfach, preiswert und umweltfreundlich hergestellt werden. Entwickelt wurde das Verfahren von der Arbeitsgruppe um Manfred T. Reetz, Direktor am Max-Planck-Institut für Kohlenforschung in Mülheim an der Ruhr. Das vielversprechende Herstellungsprinzip könnte in Zukunft die Basis für eine einfache und kostengünstige industrielle Produktion von Katalysatoren für Brennstoffzellen liefern.
„Das ist Becherglas-Chemie“, sagt Manfred Reetz über das neue Verfahren. Man merkt ihm die Begeisterung des Vollblut-Chemikers an, dem – oft nach mühsamen Umwegen – schließlich das bestechend Einfache gelungen ist. Anders als Helmut Bönnemann erzeugen er und seine Mitarbeiter mit ihrem Synthese-Verfahren keine rein metallischen Nanopartikel. Ihre Nanopartikel bestehen vielmehr aus Platinoxid (PtO2) oder aus einer oxidischen Verbindung mehrerer Edelmetalle. Erst wenn die Forscher diese Partikel auf dem Trägermaterial des Katalysators fixieren, werden sie chemisch „reduziert“, also in Metall umgewandelt.
Reine Platin-Katalysatoren werden beim Betrieb von Niedertemperatur- Brennstoffzellen mit kohlenstoffhaltigen Brennstoffen durch Nebenprodukte wie Kohlenmonoxid vergiftet. Katalysatoren aus mehreren Edelmetallen sind gegen diese Vergiftung weniger anfällig, deshalb ist es für die Forscher besonders interessant, sie zu optimieren.
Da neue Katalysator-Materialien ein wichtiger Schlüssel zu leistungsfähigen, alltagstauglichen Brennstoffzellen sind, hat das Land Nordrhein- Westfalen die Arbeitsgruppe um den Mülheimer Institutsdirektor als förderungswürdig eingestuft. Es unterstützt die Wissenschaftler im Rahmen des Verbundprojektes „Nanomaterialien als Katalysatoren in Brennstoffzellen (NaKaB)“.
Man nehme Platinsalz, Wasser, „Seife“ und erwärme das Ganze – so einfach ist das Verfahren natürlich nicht. Basis-Zutaten des Hydrolyse- Verfahrens, wie es chemisch korrekt heißt, sind das Salz des Platins, und je nach Einsatzbereich des Katalysators auch die Salze anderer Edelmetalle wie Ruthenium, Osmium oder Iridium. Diese Salze haben den Vorteil, dass sie in Wasser gelöst werden können. Die zweite Zutat ist ein wasserlösliches Tensid, das als Stabilisator wirkt. Tenside sind die wichtigsten Bestandteile von Seifen und Waschmittel – aber natürlich wird im Mülheimer Herstellungsverfahren nicht einfach Seife eingesetzt. Durch Erhitzen auf 60 bis 80 Grad Celsius in basischem Milieu entsteht eine klare, rotbraune Lösung, die mehrere Monate lang stabil bleibt und aus diesem Grund problemlos gelagert, transportiert und weiterverarbeitet werden kann.
Die Lösung enthält bereits die fertigen oxidischen Nanopartikel aus PtO2. Wenn beispielsweise reines Platinsalz verwendet wurde, sind die Platinoxid-Partikel in der Lösung etwa 1,8 Nanometer groß – optimal für den Einsatz im Katalysator. Mit diesem Verfahren lassen sich auch Mischoxide aus Platin und Ruthenium oder sogar drei oder vier Metallen herstellen. Das Mischungsverhältnis der Metalle lässt sich über die zugesetzten Metallsalze sehr gut steuern. Nanopartikel aus Platin und Ruthenium, die als wasserlösliches Mischoxid so hergestellt werden, sind 1,5 Nanometer groß.
Die Mülheimer Chemiker untersuchten die Platin-Partikel gemeinsam mit Walter Vogel vom Fritz-Haber- Institut der Max-Planck-Gesellschaft in Berlin und Wolfgang Grünert von der Ruhr-Universität in Bochum. Bei dieser Analyse stellten die Forscher überrascht fest, dass die Größe der Nanopartikel innerhalb einer ausgewählten Probe kaum variiert. Für ein so simples Verfahren ist das ungewöhnlich. Die Nanopartikel sind schließlich nur knapp zwei Milliardstel Meter groß. In der „Nanowelt“ kann eine solche Präzision sonst meist nur mit hohem technischem Aufwand erreicht werden.
Die gleichmäßige Größe der Partikel erlaubt es nun, Katalysatoren mit genau reproduzierbaren Eigenschaften herzustellen, was gerade im industriellen Maßstab außerordentlich wichtig ist. Die Lösung der Nanopartikel aus Platinoxid oder aus einem Mischoxid mehrerer Metalle kann auf zwei Wegen weiterverarbeitet werden: Eine Möglichkeit ist, sie zuerst auf den festen Träger aufzubringen und dort zu fixieren. Als Trägermaterial wird oft „Vulcan“ eingesetzt. Es besteht im Prinzip aus feinen Rußkörnchen, die zur porösen Elektrode zusammengepresst werden. Anschließend werden die oxidischen Nanopartikel durch Wasserstoffgas chemisch reduziert. Danach liegen sie als reine Metallpartikel auf der Oberfläche des Trägers und sind katalytisch aktiv. Der Katalysator ist somit einsatzbereit. Alternativ können die Nanopartikel zuerst reduziert und anschließend auf dem Träger fixiert werden.
Verklumpung ausgeschlossen
Das Beispiel im Bild zeigt oben Nanopartikel aus einem Mischoxid von Platin und Ruthenium, wie sie aus der Lösung kommen. Sie sind etwa 1,5 Nanometer groß. Unten sieht man sie als reine Metallpartikel, wie sie nach der Reduktion vorliegen. Sie sind dann etwa 1,7 Nanometer groß. Auf dem Bild ist gut zu erkennen, dass die Reduktion zu keiner unerwünschten Agglomeration, also „Verklumpung“ zu größeren Teilchen führt. Auch die Fixierung auf dem Vulcan-Träger hat keine Agglomeration zur Folge.
Noch bedarf es weiterer Grundlagenforschung, bis auf der Basis des Mülheimer Hydrolyse-Konzepts Brennstoffzellen-Katalysatoren industriell gefertigt werden können. Da die Methode einfach, billig und umweltfreundlich ist und dabei gleichmäßige Qualität liefert, erfüllt sie im Prinzip jedoch bereits jetzt wesentliche Voraussetzungen für die Großserienproduktion von leistungsfähigen Niedertemperatur-Brennstoffzellen.
Platin auf Rädern
Würden die weltweiten Platinvorräte überhaupt ausreichen, die Fahrzeugflotte der Menschheit auf Brennstoffzellen umzustellen, deren Katalysatoren Platin enthalten? Der Platinverbrauch selbst wäre kein Problem. Laut einer neuen Studie soll es etwa 46.600 Tonnen Platin allein in den Gesteinsschichten bis zu einer Tiefe von zwei Kilometern geben. Bei der Goldförderung geht man bereits tiefer. Nehmen wir an, dass es mittelfristig eine Milliarde Autos in der Welt geben wird – etwa doppelt so viele wie heute. Würden alle diese Autos tatsächlich mit Brennstoffzellen angetrieben werden, würde das ungefähr 15.000 Tonnen „Platin auf Rädern“ bedeuten. Diese Menge müsste für die Umstellung der weltweiten Fahrzeugflotte auf Brennstoffzellen nur einmal aufgebracht werden. Danach könnte ein Großteil des Platins in den Katalysatoren durch Recycling wiedergewonnen werden, schon heute sind das 95 bis 97 Prozent.
Der Ersatzbedarf durch neu gefördertes Platin betrüge bei laufender Fahrzeugproduktion etwa 62,2 Tonnen pro Jahr – bei einem durchschnittlichen Lebensalter von zehn Jahren für Autos. Heute befinden sich weltweit rund 55 Tonnen Platin in den Abgas-Katalysatoren von Autos, die bei Brennstoffzellen-Fahrzeugen entfallen würden (Quelle: World Fuel Cell Council, Frankfurt a. M.).
Quelle: https://www.weltderphysik.de/gebiet/technik/energie/brennstoffzellen/nanoteilchen/